Choosing the Right Plastic Compactor based on Waste Volume and Type of Plastic Waste
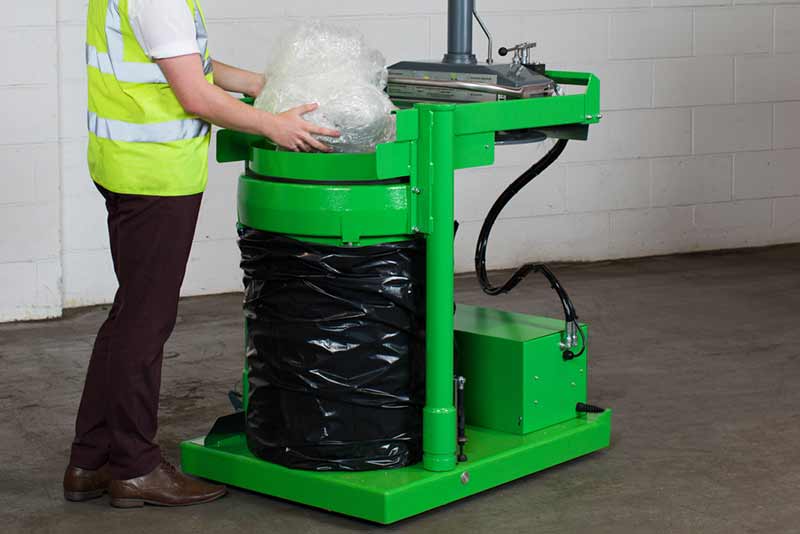
Selecting the appropriate plastic
compacting equipment requires careful consideration of your specific waste
profile and operational requirements. This guide explores how to match
compactor capabilities to your waste volume and plastic types, with a focus on
the advantages of hiring
rather than purchasing this specialist equipment. Understanding the environmental
impact of plastic waste is crucial for making informed decisions.
Assessing Waste Volume and Frequency
Before selecting a compactor, conduct a
thorough waste audit to determine your plastic waste generation patterns. Most
businesses underestimate their waste volume by 30-40%, according to recent
waste management surveys. Document both daily accumulation and peak production
periods that might require additional capacity, as recommended in the IEMA Waste Management
Guidelines.
Quantify your plastic waste in both
weight (tonnes) and volume (cubic metres) as compactors are rated using both
metrics. A simple approach is to monitor your waste collection frequency and
container sizes over a month to establish baseline figures, as suggested in how to make money from waste. Modern waste
audits often include digital tracking tools that can provide precise data on
waste generation patterns throughout your operational cycle.
Identifying Different Plastic Types in Your Waste Stream
Plastic waste varies significantly in
composition, affecting how it can be compacted and recycled according to the British Plastics Federation recycling guidelines:
●
Film and soft plastics: Packaging films, bags,
wraps (LDPE, LLDPE) - learn more about soft plastics recycling
●
Rigid containers: Bottles, tubs, trays (HDPE,
PET, PP) - see glass recycling comparison
●
Industrial plastics: Manufacturing scrap,
off-cuts, rejected products
●
Composite materials: Multi-layer or
mixed-material packaging
●
Expanded polystyrene: Packaging materials,
insulation - polystyrene disposal guidance
Most businesses have a predominant
plastic type that makes up 60-75% of their waste stream, according to RECOUP's
Plastics Recycling Overview. Identifying this primary component helps narrow
your compactor options. Laboratory testing or consultation with waste specialists can provide detailed
composition analysis if required.
Matching Waste Volume to Compactor Capacity
Small Volume Solutions (Under 5 Tonnes/Month)
For businesses generating smaller volumes
of plastic waste, equipment
sizing guidelines from WRAP recommend:
●
Compact vertical balers with 3-6
tonne pressing force
●
Cycle times of 25-40 seconds per
operation
●
Bale weights typically 30-80kg
●
Space requirements of
approximately 2m²
These solutions typically reduce
collection frequencies by 75%, generating 4-8 bales weekly that can be managed
without specialized handling equipment. For context, 5 tonnes monthly equates
roughly to 40m³ of uncompacted mixed plastics, according to resource
efficiency metrics. Smaller businesses can learn from local environmental initiatives that have
successfully implemented similar systems and could explore how to train staff on proper equipment use.
Medium Capacity Options (5-20 Tonnes/Month)
Mid-sized operations benefit from
solutions outlined in waste
industry best practice guides:
●
Semi-automatic vertical or small
horizontal balers
●
Pressing force of 8-20 tonnes
●
Cycle times of 15-30 seconds
●
Bale weights of 100-250kg
These systems produce standardized bales
that meet most recycler specifications and typically achieve 10:1 volume
reduction ratios. Integration with bin lifters or conveyor systems increases
throughput efficiency in this category. For businesses handling both plastic
and cardboard, dual-purpose balers offer excellent
versatility, similar to those discussed in the article on businesses selling cardboard waste.
High Volume Industrial Solutions (20+ Tonnes/Month)
Large-scale operations require equipment
that meets specifications in the Environment Agency's technical guidance:
●
Fully automatic horizontal balers
●
Pressing force of 25-100 tonnes
●
Continuous feed capabilities
●
Bale weights of 300-650kg
These systems often connect directly to
production areas, capturing waste at source and minimizing internal handling.
The latest models incorporate Industry 4.0 features including predictive
maintenance, remote monitoring, and detailed material tracking as detailed in manufacturing
technology reviews. For large-volume operations, understanding Britain's plastic waste journey can help
contextualize the environmental impact of your waste management decisions
alongside recycling facts and figures.
Cost-benefit Analysis at Different Volumes
The economic case for compaction
strengthens with volume, as demonstrated by cost-benefit
analysis from Zero Waste Scotland:
●
Small volume: Typical savings of £200-600
monthly through reduced collections
●
Medium volume: Returns of £500-2,000 monthly
through combination of reduced disposal costs and potential rebates for
material
●
High volume: Potential returns of
£2,000-8,000+ monthly when considering logistics, disposal, and material value
Most hire arrangements become
cost-positive at approximately 2 tonnes of plastic waste monthly, with typical
payback periods of 2-3 months for the initial setup investment. Similar to how businesses can make money from cardboard waste,
properly baled plastic can often generate revenue rather than disposal costs, a
point emphasized in commercial
waste valuation reports.
How Different Plastic Types Affect Compactor Choice
Soft Plastics (LDPE, Plastic Film, Packaging) Requirements
Soft plastics present unique challenges
according to RECOUP's
plastics processing guidelines:
●
Tendency to trap air during
compression
●
Potential to spring back after
initial compaction
●
Often contaminated with labels or
tape
Effective compaction requires:
●
Perforation systems to release
trapped air
●
Multi-stage compression cycles
●
Higher compression ratios
(typically 20:1)
●
Specialized binding methods to
maintain bale integrity
Recent advancements in film compactors
have improved density outcomes by 35%, making soft plastics recycling economically viable
for previously problematic materials. According to the British Plastics Federation, soft plastic
recycling rates have improved by 22% since 2023 due to better collection and
processing technology. For businesses looking to optimize their approach to
soft plastics, cardboard shredding principles can sometimes
be applied to plastic film conditioning.
Hard Plastics (HDPE, PP, PS) Considerations
Rigid plastics require equipment
specifications outlined in ISO
18616 for plastics recycling:
●
Higher pressure systems
●
Abrasion-resistant compression
chambers
●
Optional pre-crushing capabilities
for hollow containers
●
More robust hydraulic systems
These materials typically achieve
compression ratios of 6:1 to 8:1, with modern systems capable of producing
mill-sized bales directly acceptable to reprocessors without additional
handling. For securing these denser bales, appropriate bale strapping is essential. The processing of
rigid plastics shares some similarities with glass recycling in terms of handling
considerations.
Mixed Plastic Waste Solutions
For businesses with diverse plastic
streams, WRAP's
mixed plastics protocol recommends:
●
Multi-setting programmable
compactors adjust parameters by material type
●
Dual-chamber systems allow
segregation of high and low-value plastics
●
Intelligent compactors with
material recognition capabilities optimize settings automatically
When handling mixed plastics, equipment
with adjustable pressure control prevents damage to the machine while
maximizing density across different material types. Understanding recycling facts and figures can help
prioritize which materials to separate for maximum value. Similar principles
apply when disposing of cardboard waste alongside
plastics.
Speciality Plastics Handling
Challenging materials require specialized
approaches as detailed in the Plastics Recyclers Europe technical guidelines:
●
Expanded polystyrene needs crushing before
compression
●
Nylon and engineering plastics may
require higher pressure capabilities
●
Contaminated plastics might need
washing integrations
●
Bioplastics and compostables
require specific handling protocols
Hire specialists can provide
application-specific equipment configured for these unique challenges, often
unavailable through standard purchase channels. For businesses looking to
improve their environmental credentials, integrating these solutions can be
part of educating about sustainability, similar to initiatives in schools.
Your next steps
Selecting the appropriate plastic
compactor based on your waste volume and plastic types dramatically improves
waste management efficiency while delivering significant cost savings. Hiring
arrangements provide flexibility, expert support, and access to the latest
technology without capital investment.
Contact
our specialist team today for a comprehensive waste audit and
personalized recommendation on the ideal plastic compactor solution for your
business needs.